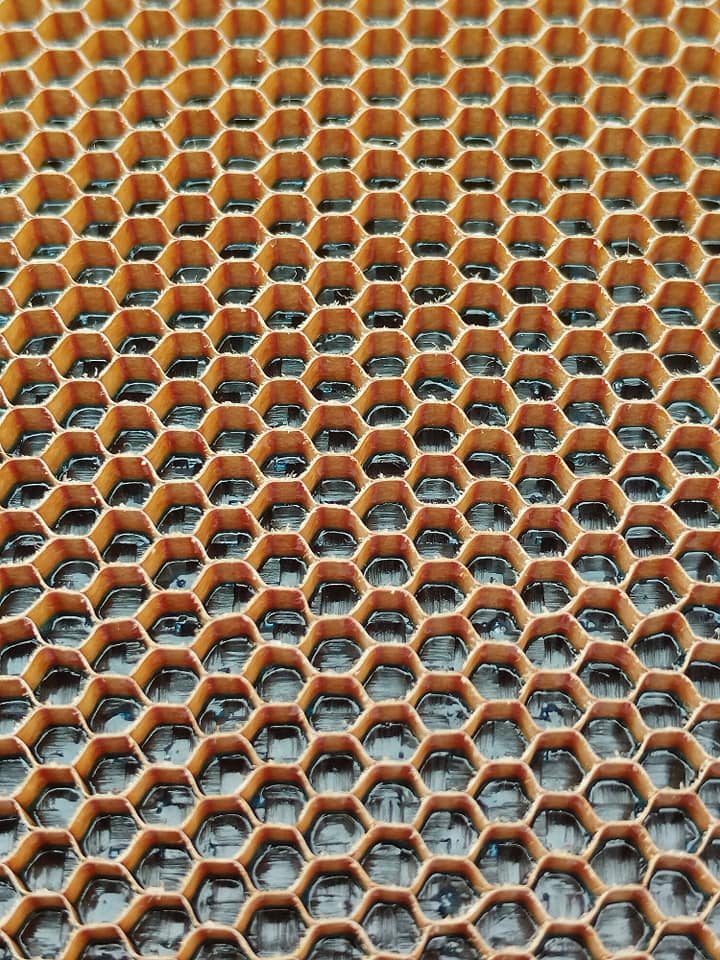
The boards are made entirely of epoxy resin and 48kg carbon fiber/ 3mm aramid honeycomb sandwich.
To ensure the foil’s solidity and reactivity, the box is made of 80kg airex, connected to the deck by two 25mm blocks and all carbon-fibered. I use 10′ Chinook rails which, if not light, are unbreakable. FCS rails can be fitted on request, for a weight saving of 125g; or 17″ Chinook rails with an additional weight of around 100g.
Around a core of EPS foam, density 10 or 15kg (to be defined when ordering), machined on a digital machine and entirely finished by hand, I make a total sandwich of the board, alternating a layer of carbon fiber, the honeycomb and again a layer of carbon.
An additional layer is added to the sandwich at the feet and foil case to significantly increase compressive strength.
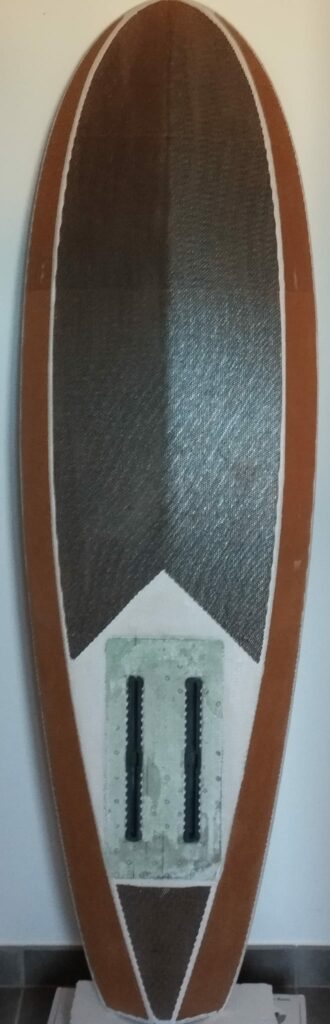
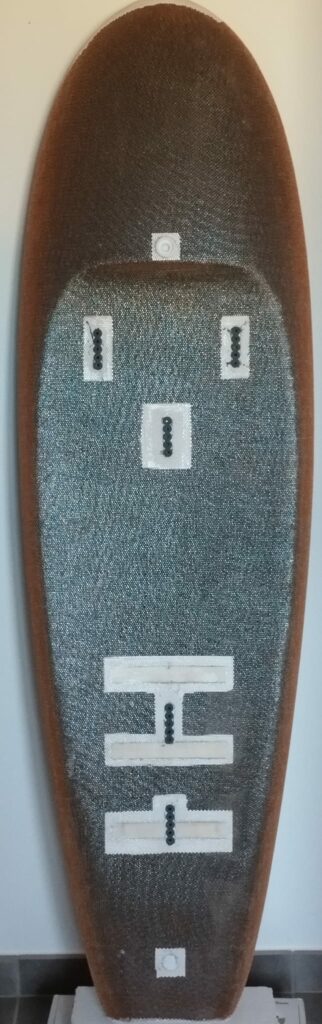
A new layer of carbon is added on top, as well as an additional layer of fiberglass on the deck. All these operations require the board to be vacuum-pressurized 4 times.
The fibers are high-grade 160g. At its thickest, this results in a total quantity of 800g. (By comparison, the standard boards of the major brands are around 280g).
Finally, the finish and color are achieved with tinted epoxy and a coat of transparent matt varnish.
US Rails Weight:
Chinook 10’ 390g
Chinook 17’ 476g
Futur 266g